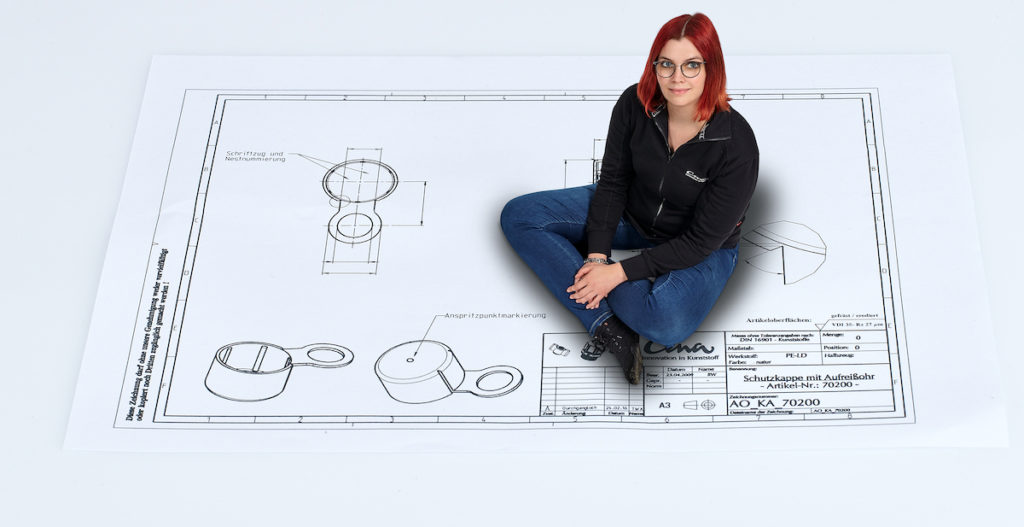
Product development
Small parts, big effect. The most important basis is a plastic-compatible article design, early, open communication with the customer and joint coordination of the requirements for the article. Take advantage of the experience and individual advice of our specialists with regard to material selection, functionalities and tool design. This is where there is great potential for savings. We have been developing sophisticated injection moulded parts and assemblies for more than 80 years, across all industries.
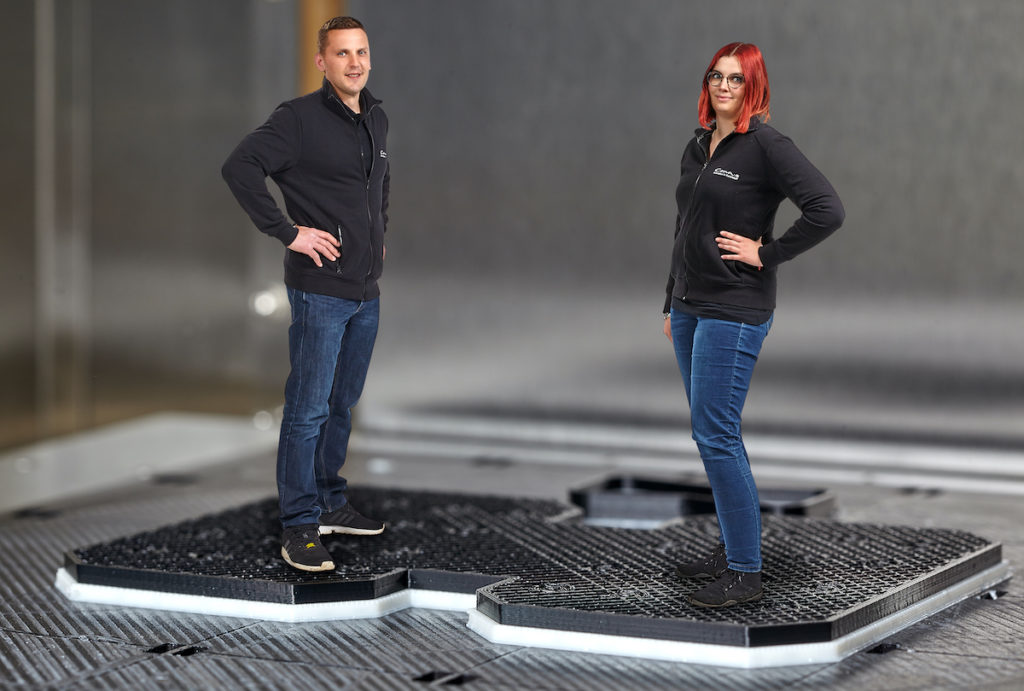
Rapid prototyping
3D printing has changed the possibilities for creating functional patterns dramatically. Materials, processes and manufacturing times are subject to permanent change and progress. Today, 3D printing has a different status compared to conventional Rapi-Tooling. Since 2011, we have had a 3D printer in house to create 3D prototypes, and since 2018 an FDM printer.
On request, we will create a 3D prototype of your component/assembly. Other options for quickly obtaining meaningful components and assemblies are SLS prototypes or PUR vacuum cast parts from silicone moulds or prototypes in original plastic, injection-moulded in a casting resin tool. Multi-component (2K) prototyping is also possible.
3D printing does not replace the creation of a complete injection moulding tool made of steel, among other things, but in many cases 3D printing flanks a steel prototype tool for the validation of the component functions. We have been offering this to our customers in short manufacturing times for years.
Depending on the level of development and requirement: we offer a wide range of prototyping to fit every phase of your project and budget.
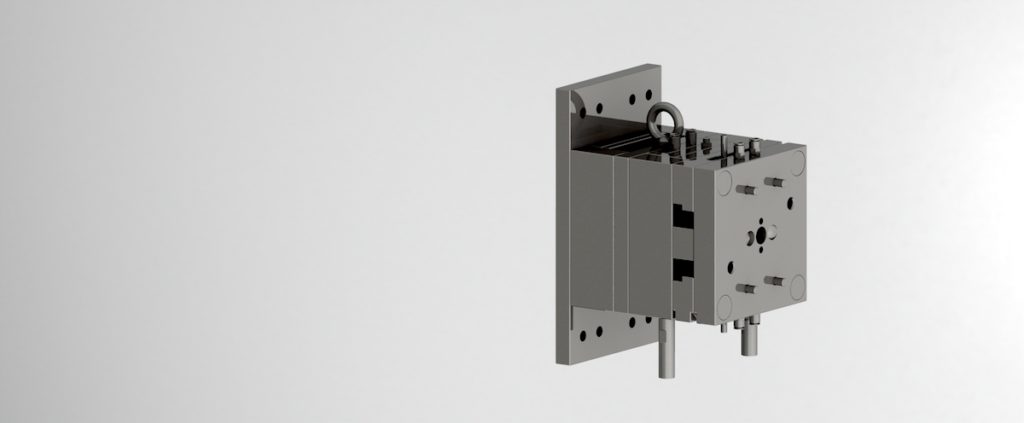
Tool design
At CENA, tools have been designed in-house since the beginning in 1933 according to our own design standards and constantly growing knowledge. Article data and tool data remain in one hand - no information goes to third parties.
The use of modular tools that can be flexibly expanded reduces tool costs and procurement times for our customers.
The use of Moldflow simulation software for the optimal design of the mould and the article is a matter of course. The tool design is paperless - purely digital, as is the data transfer to the mould making department.
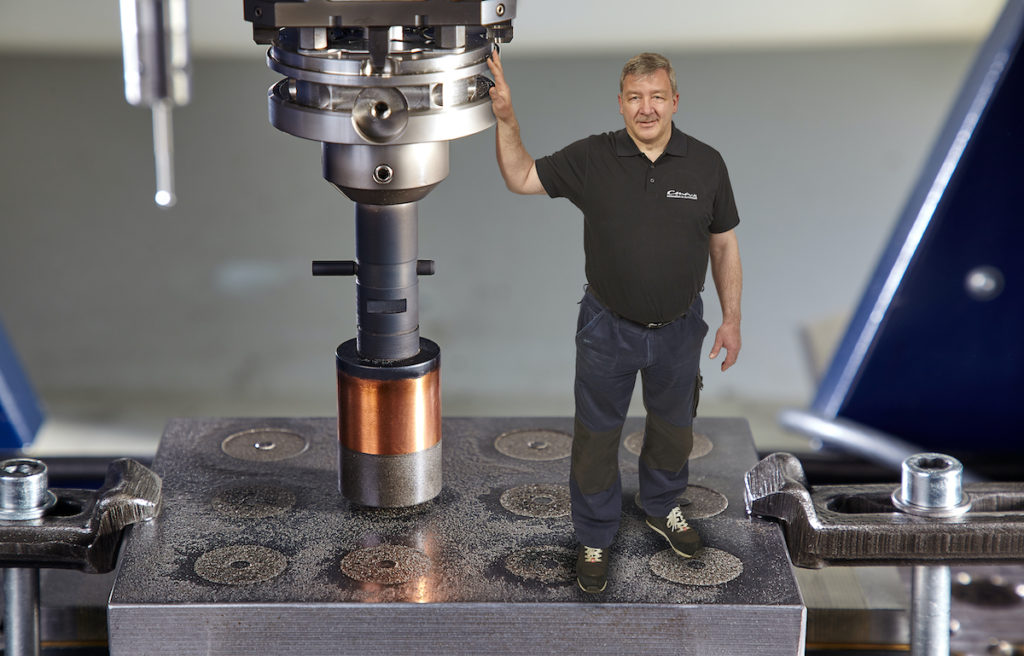
Tool and mould making
The construction of the moulds/tools is handled via established CAD/CAM interfaces. Our expertise lies in particular in the creation of filigree, repeatable structures such as internal/external threads in the smallest dimensions.
Precision is the prerequisite for ensuring the desired properties of the plastic component.
Depending on the component and customer requirements, we implement the article design in individual moulds or in modular master mould concepts. Our master mould concept includes hot runner system, gear system, slider-tool system and is subject to constant expansion and optimisation. The advantages of master mould systems are the low manufacturing costs and the short delivery times until series production is ready.
Our tools are stored in a fireproof tool store.
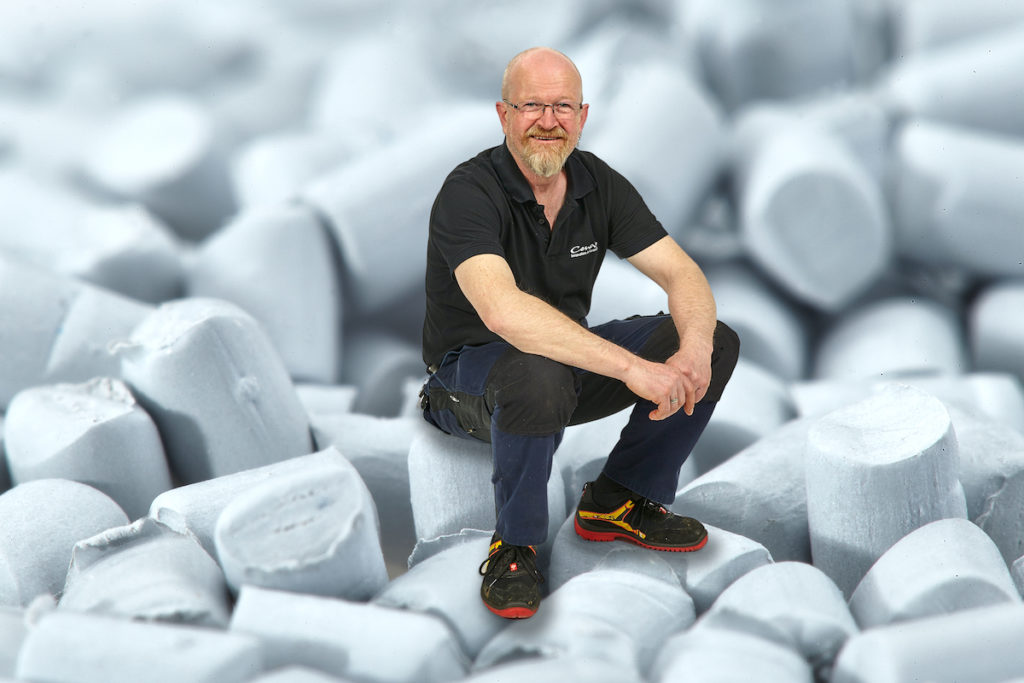
Plastic injection moulding
We produce small and large series in our fully automated injection moulding shop. All injection moulding machines, the peripheral equipment and the supply facilities are computer-monitored and are switched off in the event of deviations in order to maintain the production conditions and thus the quality at a constant level. Our production machines are basically designed and equipped in the same way, so that redundant machines are available in every clamping force size. This represents an important building block in terms of fail-safety. The production machines are connected to the inventory control system via a central computer and are monitored in real time. The clamping force sizes range from 35 t to 100 t with shot weights from 0.5g to approx. 80g.Our material range extends from the classic polyolefins (LD-PE, HD-PE, PP) to engineering plastics such as PA 6.6, PA 12, PA 6.6 30GF, PCT, PC, ABS, PBT, POM, and soft plastics such as TPEs in various grades. Additives such as flame retardants, UV protection, conductive, antistatic, etc. and colour variants according to customer requirements are also available.
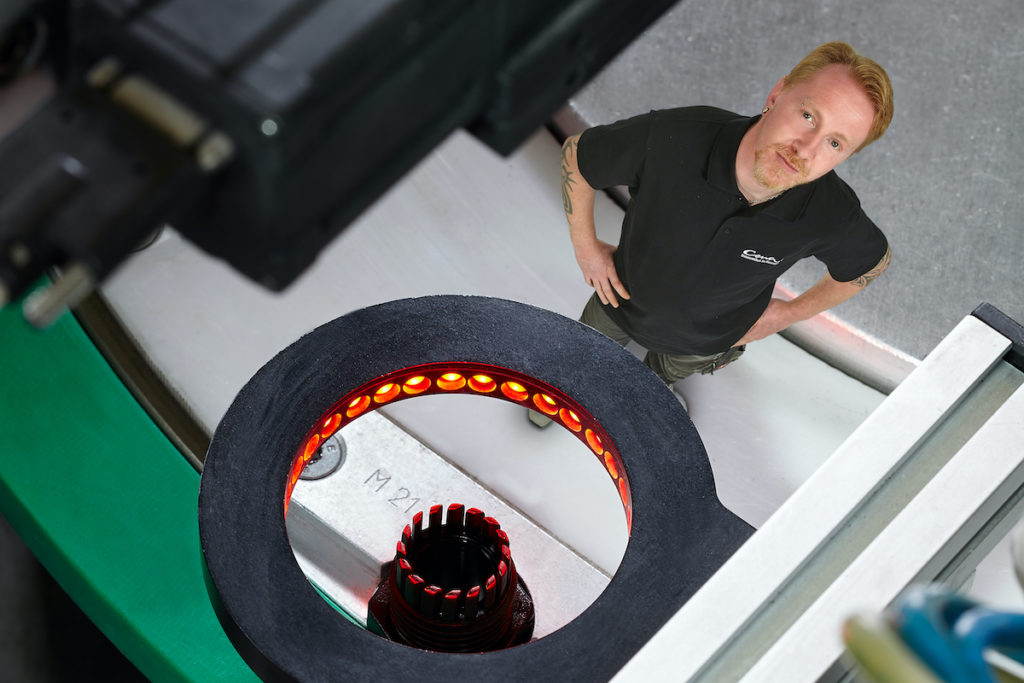
Assembly & Packing
Another important component in our range of competences is the area of automated assembly and packaging, because it is only here that functional assemblies can be economically produced in large quantities from individual parts. Our automations monitor and measure the quality of the individual parts and the result of each assembly step. Defective parts or process steps lead to the rejection of the n.o.k. part. part. This means that the automated assembly process is 100% monitored - an important quality feature of Cena Kunststoff GmbH.
In the field of automated packaging, we offer our customers small-packed single-brand articles in customer-specific PU, individually designed imprints, logos, barcode and/or QR code.
In addition, we offer the packaging of sets (with up to five different components in any number) in individually configured polybags. Here you can additionally choose Euro perforation, double welding, with/without perforation.
We would be happy to talk to you about your requirements and expectations with regard to logistically sensible packaging solutions.
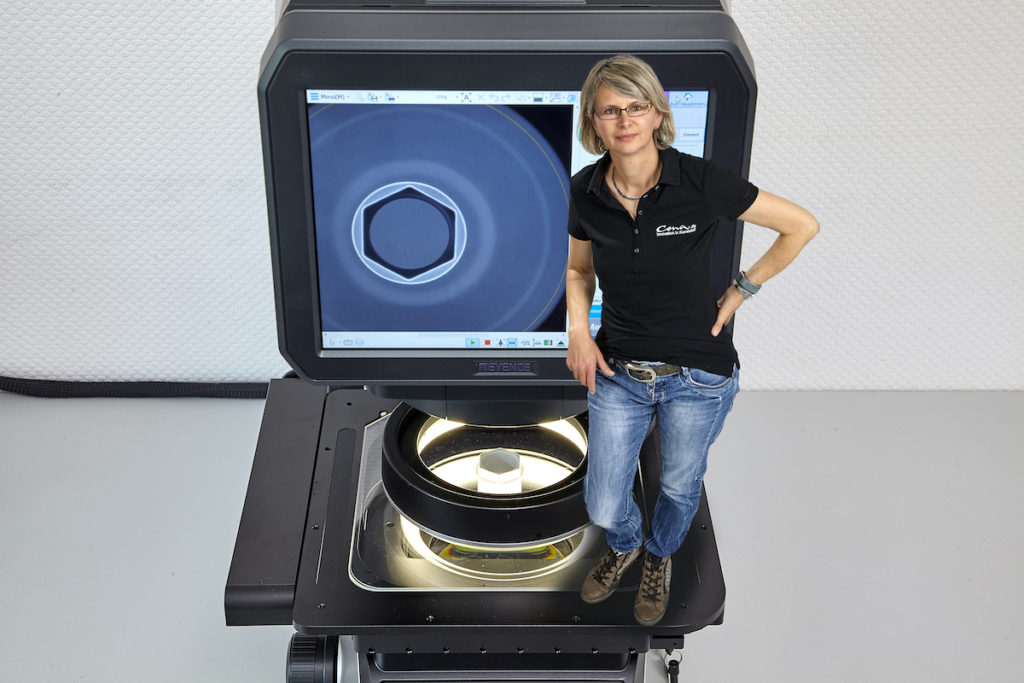
Quality
Alongside trust, reliability and innovative strength, quality is the most important pillar of our company. In our company history, we have repeatedly set quality standards for the industry. The quality of the products and the continuity of the processes are ensured by a reliable and demanding quality management system according to DIN EN ISO 9001.
The company's promise also includes high quality standards in delivery capability and service. We facilitate the daily work of our customers at home and abroad through the rapid availability of our products, moderate stocking and extremely efficient logistics.
This high quality of delivery and service is one of the reasons for the high level of customer satisfaction and high continuity in business relationships.
We are always available for our customers through our Technical Advisory Service and Sales Department.
Our technical equipment for ensuring and monitoring quality is constantly being adapted to technical innovations. For example, we have recently expanded our CAQ system with additional functionalities. Our CAQ system is used for the complete processing of complaints, including the 8D report. Inspection plans, control plans and EMPBs are also handled in this CAQ system.
As an extension and for permanent quality assurance accompanying production, we have been using a tensile testing machine and a digital measuring projector since 2020.
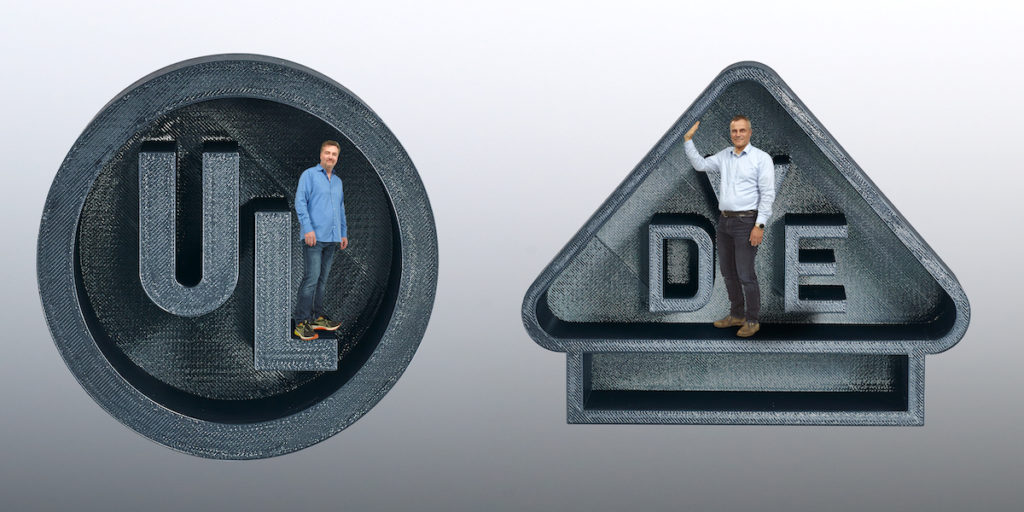
Approvals
For our catalogue products in the area of cable glands, we acquired approvals according to VDE and UL several years ago, expand these with new products and constantly maintain them at the respective valid status. As an important service, we offer the approval of cable glands and assemblies according to customer requirements on behalf of the customer. We take care of the project from the design of the article or assembly to the approved marketable end product for the customer. We have approvals according to VDE 62444, UL 514B, UL 514A, CSR
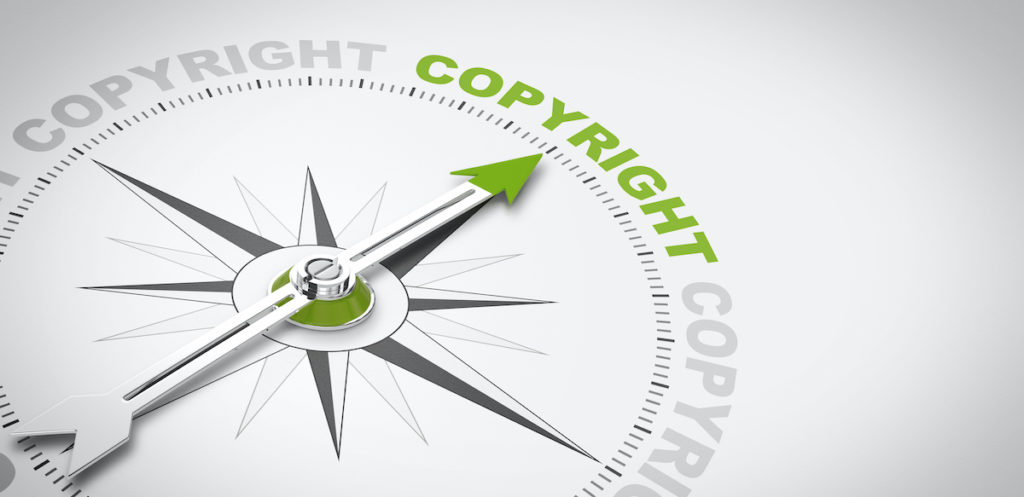
Patents - Property rights
We always try to flank new developments with property rights and patents.
You can find news and innovations on our homepage NEWS.